How wire-to-water efficiency testing can extend the life of your pump systems
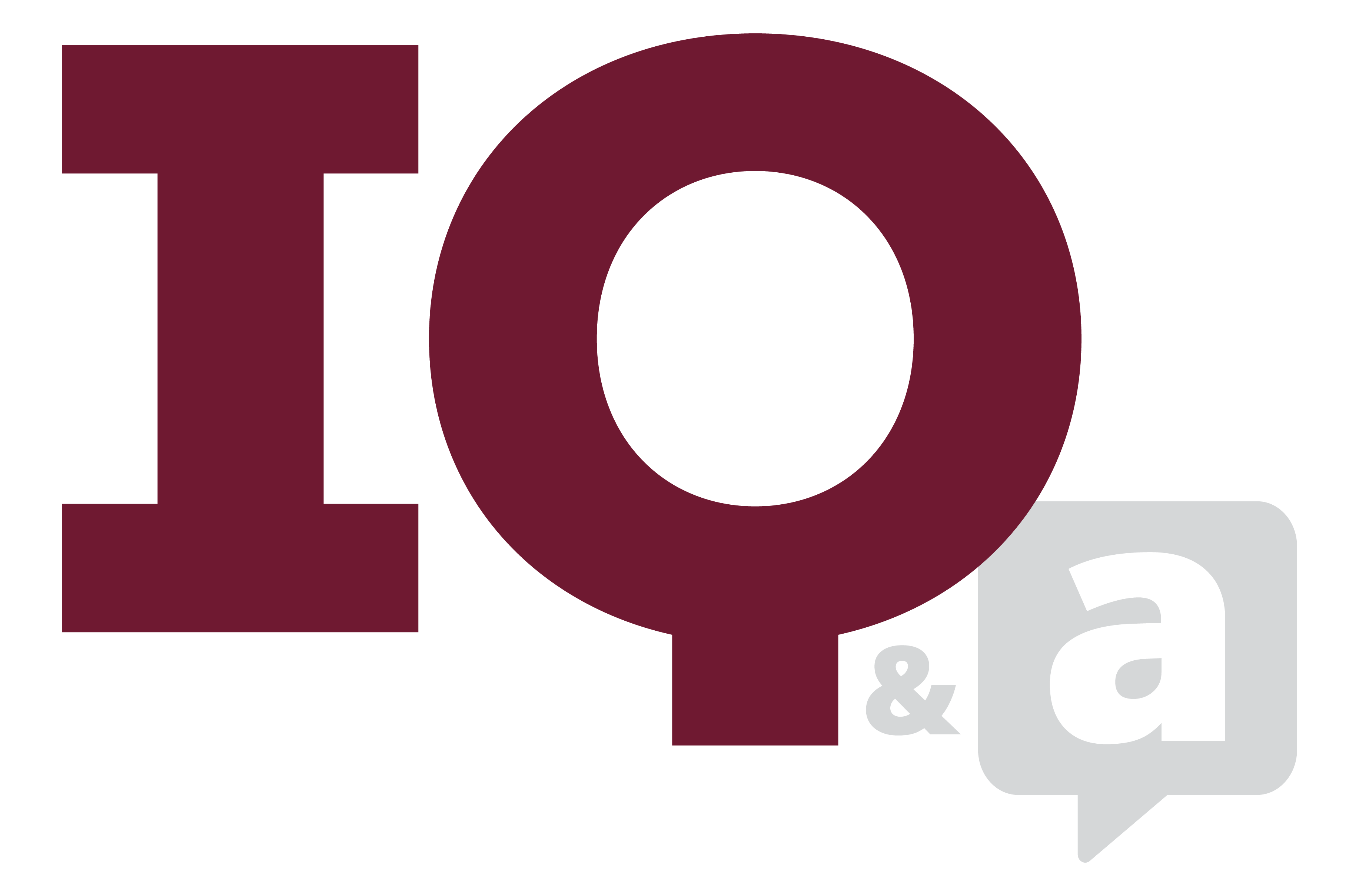
Pumps are more than just at the heart of water infrastructure – they are the heart. If anything is misaligned, if the ratio of input power to output power is slightly out of sync, the entire body is at risk of failing. Which is why wire-to-water efficiency testing is so very important to a healthy system.
In this IQ&A, Garver’s series of conversations with leading experts delivering value to communities across the country, Water and Energy Practice Leader Eric Dole, PE, PSAP, discusses the role of the pump in water, wastewater, and power generation systems, the importance of wire-to-water efficiency, and the measures that clients can take to extend a pump system’s life.
What is wire-to-water testing and how do you use it to develop energy efficiency measures?
Wire-to-water efficiency testing is the ratio of a pump’s water horsepower output (numerator) to the kilowatt input to the motor (denominator), after converting units so they’re the same. For example, it is a way to determine how much electrical power (denominator) is used to move water at a certain flow and total head (numerator). Pumps driven by variable frequency drives (VFDs) use the same ratio, but the denominator is the kilowatt input to the VFD, instead of the motor. Wire-to-water efficiency is an excellent surrogate to determine the electro-mechanical fitness of a pump and to establish a field verified system curve. However, if not performed correctly with the proper QA/QC checks along the way, it can lead to erroneous results. The output of a wire-to-water test reveals the shape of the pump curve, system curve, and wire-to-water efficiency as a function of flow. Understanding where the pump curve intersects the system curve can identify what is happening in the pump system and how to improve the pump efficiency.
Why is pump optimization so important?
Pumps are the heartbeat of water, wastewater, and power generation systems. Furthermore, optimized pumping is the easiest way to reduce energy and maintenance costs, while increasing reliability.
How does a key performance indicator (KPI) gauge equipment fitness?
KPI energy dashboarding provides useful, real-time data to gauge the fitness of the pump system. This only works when normalized to a process metric such as totalized flow or wire-to-water efficiency. If the KPI dashboard is not properly designed and installed, and the instruments it relies on are not frequently calibrated, it will not give you reliable and accurate data to make decisions. It follows the saying “garbage in equals garbage out.” However, when properly designed, installed, and its instruments are properly calibrated, KPI dashboarding for wire-to-water efficiency (%) or energy intensity (kWh/MG) can give a pump operator invaluable data. It makes the unseeable seeable and allows a pump operator to correct any actions before they become irreversible damage, consuming excessive data along the way.
In one example, both 300 HP pumps pumped 5 MGD of sewage out of the wet well to a downstream manhole three miles away and 110 feet higher in elevation through a 16-inch force main. Pump 1 was much more efficient and consumed less kWh/MG than Pump 2, but both pumps had identical pumping conditions. The KPI dashboard alarmed and notified the operator of the low wire-to-water efficiency overnight. The alarm locked out the pump when such a drop in wire-to-water efficiency occurred over a short period of time. The operator immediately pulled Pump 2 and noticed there was debris clogging the volute of Pump 2. Thanks to the KPI dashboard, catastrophic pump failure was avoided.
What is the best way to right size and optimize pumps so that clients gain the most out of their system?
The pump curve should intersect the system curve in the preferred operating region (POR) of the pump to optimize pumping. Operating the pump outside of the POR will result in excessive energy consumption, increased maintenance, and decreased reliability.
Is there something clients can do to preserve the long-term operation of their pumps so they can maximize their investment?
There are five main things clients can do to increase the life of a pump system:
- Properly design the pump system so the pump curve(s) intersect the system curve in the POR.
- Always pay attention to net positive suction head available and net positive suction head required by the pump to avoid cavitation.
- Develop a control scheme that turns the pump on when the pump curve intersects the system curve to the right of the POR, allowing the pump to ride through the POR and turn the pump off to the left of the POR.
- Know your current and future operating conditions with respect to flow to plan for the correct combination of pumps because rarely will one pump do it all even with a VFD.
- Install KPI energy dashboarding on all pumps to monitor the electro-mechanical fitness of a pump system.
Is there a minimum pump horsepower that does not make a good candidate for wire-to-water testing or KPI dashboarding?
Most electric utility companies do not offer demand side management (DSM) rebates for pump optimization / wire-to-water efficiency testing under 40 HP. If you have a pump less than 40 HP that plays a critical role in your treatment process / distribution system / raw water delivery system / collection system and a catastrophic failure would result in unwanted downtime, then integrate KPI trending in the pump system.
To learn more about what Garver’s Water Technology Team can do for you, visit our Water Technology Team page.
Share this article