Streamlining Wichita
Collaboration and Owner’s Advisor services changed the workflow for Kansas’ largest water treatment plant.
In Wichita, Kansas, and neighboring communities, more than half a million people turn their taps each day and expect clean water. It’s not by the virtue of magic that such a feat is accomplished, but by the sheer power of engineering that makes this possible. And now, Wichita’s new water treatment plant – the state’s largest – and one of the largest WIFIA-funded programs in the United States today, will replace an aging 80-year-old plant, providing the growing community with a source of safe, reliable water for decades to come.
The sheer size of the plant, which can be measured in terms of football fields, requires more than just excellent engineering. It requires collaboration among numerous stakeholders, coordination of regulatory authorities, funding navigation, and careful coordination so that the communities’ interests are always maintained.
So, how do you keep a project of this magnitude on track and successfully moving forward? Alternative Project Delivery (APD), more often referred to as Collaborative Project Delivery (CPD) in the water industry, combined with utilization of an Owner’s Advisor (OA). While CPD fosters engagement of contractors earlier and promotes partnering with consultants to produce an efficient design, the OA acts as an extension of the owner’s staff to maintain their best interests and keep design criteria in alignment with project goals and objectives.
As the OA during basis of design development, Garver helped identify a slightly different design approach to effectively meet Wichita’s goals. Rather than having a different treatment train for each source, Garver suggested using one that would be more efficient and reliable for the long term – with a firm capacity of 120 MGD – and capable of treating all three sources. That suggestion ended up being a $100 million idea, dropping the projected construction cost from $600 to $500 million. Still, CPD’s work doesn’t stop there.
After the aforementioned money-saver, the owner decided to retain Garver’s services for the second phase of the project. If the first phase was the project outline, then the second phase fills in details and implements the work. CPD allows for construction to commence as design packages are completed. The OA furnishes the owner with resources to keep up with the pace and provide objective expertise for areas outside the staff’s comfort. This includes design reviews, overseeing progress of deliverables, identifying opportunities to improve treatment efficiencies, and finding potential cost savings.
"As Wichita’s trusted advisor, we care about them receiving the best solution for the best use of their budget."
Kyle Kruger, PE
Water Implementation Leader
“As Wichita’s trusted advisor,” Water Implementation Leader Kyle Kruger, PE said, “we care about them receiving the best solution for the best use of their budget. One that lasts for generations to come and that everyone involved can be proud of.”
The presence of an OA is especially key in situations where the Design-Build (DB) approach has been taken, meaning there’s just one contract for the designer and builder.
The DB approach means the designer and builder work collaboratively to make sure the design is constructable and easily implemented. This method also requires more oversight from the OA to serve as the quality check for design deliverables, making sure they align with the goals and needs of the owner.
Still, the significance of the project is how it will support the community for decades to come.
“It means a lot,” said Garver Kansas Water Team Leader Mark Dolechek, PE. “It’s going to be a project that serves me, my family, and future generations to come. Because this is still going to be here even after everyone involved is long gone.”
CPD Water Works
Wichita isn’t the only project on which Garver’s Water and Wastewater Team has utilized APD/CPD methods to streamline the design and construction processes for its clients. Here are a few ongoing examples of when APD/CPD allowed the firm to go above and beyond expectations.
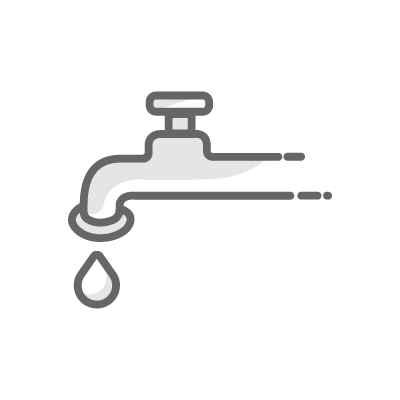
Enid Kaw Lake Water Supply Program
Enid, Oklahoma
Recent legislation in Oklahoma made it possible for the Enid Kaw Lake Water Supply Program, a $317 million capital project, to utilize the Construction Management-At-Risk (CMAR) CPD method. It represents the state’s first use of CMAR and allowed for upfront collaboration between the design team (Garver) and the City’s construction manager (Garney Construction).
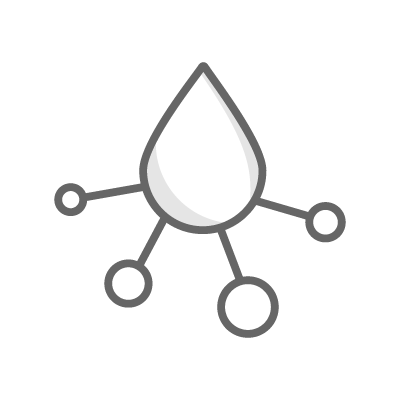
Pflugerville Water Treatment Plant Expansion
Pflugerville, Texas
As the OA (also referred to as Owner’s Representative), Garver established design criteria to minimize the WTP’s footprint, optimized the lifecycle of the filtration membranes, and created a more resilient facility to handle water quality changes. Garver has also supported the City with determining the best procurement approach for each project portion, to align with bringing the new systems online in time to meet rising demands (the raw water line is using CMAR delivery).
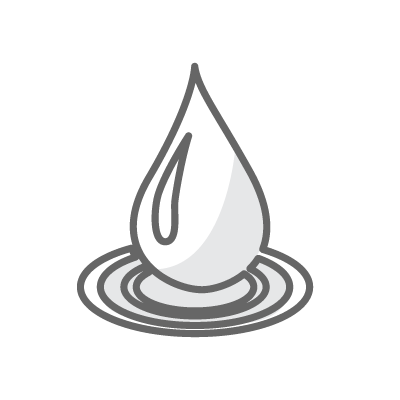
Norman WRF IPR Pilot
Norman WRF IPR Pilot Norman, Oklahoma
As Oklahoma’s first potential potable reuse application, the City of Norman’s Water Reclamation Facility is going to great efforts to evaluate treatment alternatives and demonstrate an effective process train. Garver helped the City secure BOR Title XI funding and identified how using design-build delivery would efficiently implement a robust demonstration project with large scale biological nutrient removal processes and multiple pilot-scale tertiary treatment packages to meet a tight schedule.
Share this article