How BNA took a sustainable approach to on-site pavement recycling
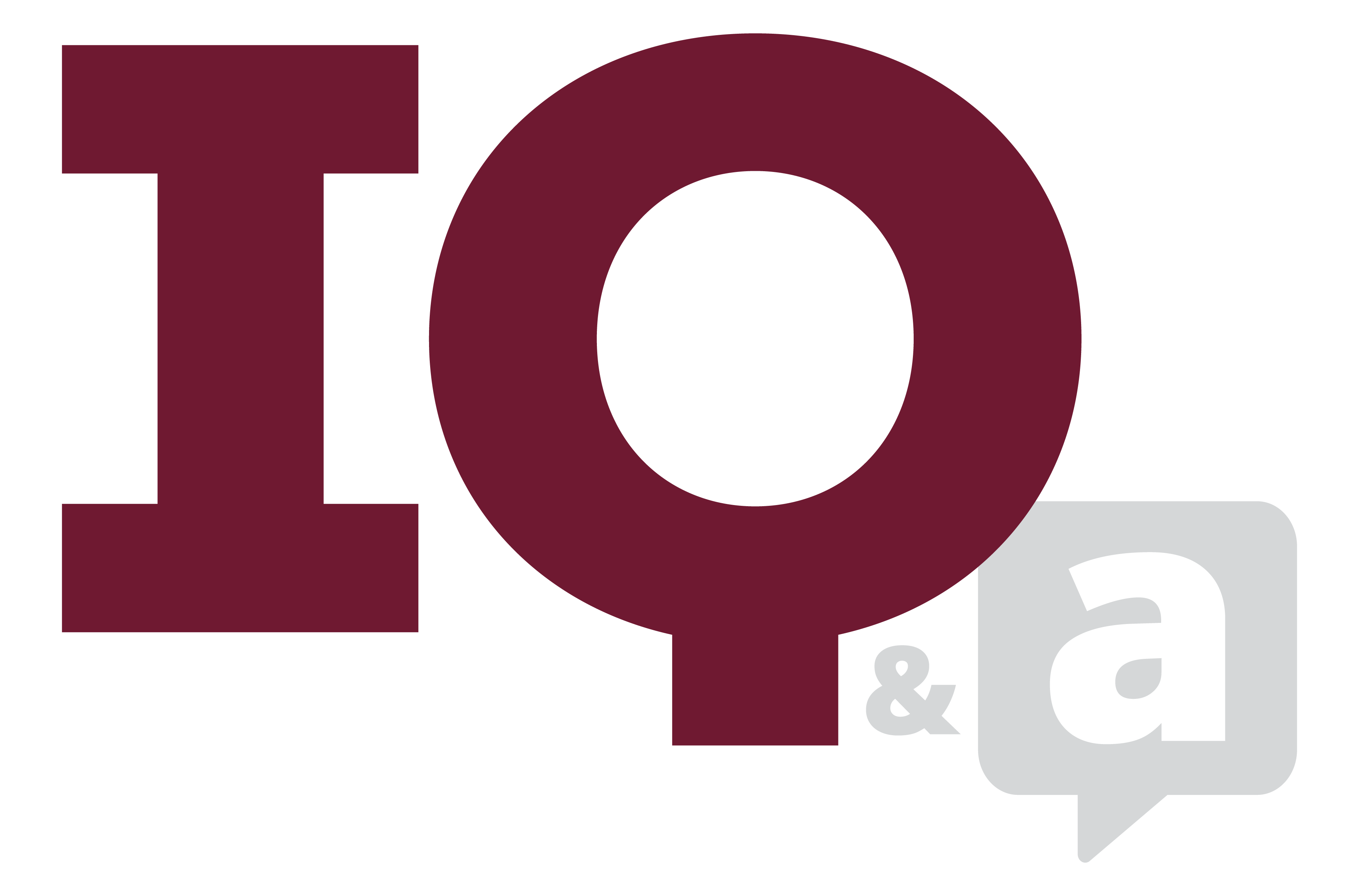
Nashville International Airport has never been a stranger to innovation. In recent years, Garver has partnered with the airport on a number of forward-thinking projects, including a geothermal exchange system, the largest of its kind in North America, which cools roughly a million square feet of terminal space and saves the airport $600,000 in annual electrical costs. In that sense, they’ve been able to invest in long-term resiliency and sustainability. And recently, they took it another step further.
On a recent project at BNA, Garver East Region Aviation Leader Ryan Sisemore, PE, and Garver’s Aviation Team realized they had an opportunity. They were tasked with rehabilitating Runway 2R-20L, the “workhorse of the airport,” as Sisemore described it. But rather than approaching the $65 million project with a traditional fix, they realized that certain parameters made the green approach not only more sustainable, but more cost effective as well. In real terms, this meant recycling a quarter-million tons of pavement.
In this IQ&A, Garver’s series of conversations with leading experts delivering value to communities across the country, Sisemore discussed the technology that the Garver Aviation Team utilized, the challenges they faced, and the future of sustainability on the airfield.
What made this approach the best one at BNA?
It's difficult – near impossible, really – to say to a client, ‘We want to incorporate a lot of sustainable construction practices in this job and it's going to cost you an extra 15%.’ On a $50 million job, you're not going to find many clients who are going to be like, ‘Yeah, let's do it.’ But if we can find those opportunities where sustainability meets the construction timeline and the project budget, it can work.
In Nashville, by reclaiming materials from the existing infrastructure, we not only saved a lot of time by having all of the material on-site, we also saved a lot of money because they didn't have to quarry and process virgin aggregates – bringing them in and then hauling off and wasting the old pavement. Everything was right there on-site, so we could actually speed up the pace of construction and trim the budget a bit using a sustainable technique.
It's rare that that happens. This is one of those rare instances where sustainability helps meet the schedule and budget in a positive way.
How widely used is this technology?
We operate in an ultra-safe environment, a very conservative environment, so the FAA typically will take their time adopting any type of new construction technique. You'll usually see it in roadways before you see it at an airport.
That’s why, when material reuse really got started, we saw it occurring first at the general aviation level. It started with a lot of asphalt reclamation, or full-depth reclamation, which is where you mill asphalt in place – adding cement and moisture, shaping, rolling, and curing that as a new base for the fresh asphalt on top. And then we started to see reclamation at the air carrier level with the P-219 specification, which allows you to use crushed and processed concrete as the crushed aggregate base course.
Nowadays, though, these techniques are the norm. Ten years ago, there were a lot of people who were still adopting the technique; there were still contractors who were getting up to speed. Because it doesn't matter what we design if we don't have the construction community who can do it. Eventually, we had specialty contractors come along, people who knew the techniques, who had the equipment, who had the requisite knowledge to go do it. This is by no means state-of-the-art anymore. But what we're seeing is that it’s becoming more of a typical construction practice. We’re seeing it used in wider arrays. We're kind of still expanding on it.
How did this chosen technique help contribute to the project’s sustainable benefits?
This runway was built 30 years ago and it’s BNA's most heavily used runway – it’s the workhorse. It’s also Southwest’s preferred runway, because it provides a short taxi from Concourses C and D – their gate locations – to the runway. After 30 years of performing well, the runway had reached the end of its service life. With this project, we had an opportunity to reexamine the exit taxiway locations from the runway for the modern fleet and to balance the runway occupancy time, which is the time from when an airplane crosses the threshold until it clears the runway.
Because of the location of this runway, we were able to completely fence the project out of the Airport Operations Area. For most airport projects, you're in the middle of the airport environment. There are aircraft all around you, and everyone must be badged. It can be challenging to build on an active airport. In this case, our crushing and screening operation was literally just hundreds of feet from the runway. They were bringing the demolished concrete over, crushing and screening it, and then placing it right back into the runway. It was literally like a big revolving circle.
All of this gave us the ability to leverage those green techniques by even making them greener. It's all about the haul, right? The less you're moving that material, the less fuel you're using. The closer you can keep it to the site, that’s where you can reach higher levels of sustainability.
Consider all those trucks that we’re keeping off the roads – hauling material off, bringing in those quarried aggregates to the airport. The local roads were saved from much of that. There were new construction materials that came in, obviously – a lot of new concrete pipe, electrical materials, and then the new concrete at the top – but so many of the materials were right there. They needed to be processed, but they were right there for the taking.
What challenges are there in working with recycled concrete?
Well, here’s the thing: Not all concrete is the same. You might have concrete from California or Denver or New York or Florida or here in Nashville – and there are going to be changes in the original material components. So, when you start breaking down the concrete to repurpose it, you have to watch out for things that would create a non-ideal situation, such as producing too many fines, or you’re producing too few.
Then you’ve got to make sure the material is sound, because we’re taking that concrete and we're processing it and now saying, ‘Hey, this is as good as a quarried limestone aggregate.’ But is it? Does it have that durability? Will the strength serve as required? And so you have to test to make sure that your fines are being met, that you're not creating flat, elongated pieces and that the soundness of the aggregates is where it needs to be. You've just got to do your homework and make sure that the product you're building with is as good as if it were built from a virgin aggregate.
Plus, there’s a reaction that can happen inside of existing concrete called ASR, or alkali silica reaction, where concrete degrades from the inside out. And in the increasing presence of water, it really becomes exponential. It's a very challenging situation if you have ASR in your concrete. That’s a reason why the industry has been really wary of reclaiming concrete, because it's like, ‘Oh man, I don't want to put that stuff into my new pavement section.’
But what we found is that, particularly in the aggregate base course, there's still plenty of voids. If there's some small amount of that reaction still occurring, it will perform just fine. So, if there are trace amounts of ASR in concrete, which most have, it's still a candidate. You don't have to rule it out. You no longer have to say, ‘Hey, we've got ASR over here. We can't use any of this. It's all got to go to a landfill.’ But that's not the case. We can actually work with pavements with limited amounts of ASR.
To learn more about innovative runway rehabilitation methods, contact Ryan below.
Share this article