Garver’s tailored approach to optimizing underground aircraft-rated structures
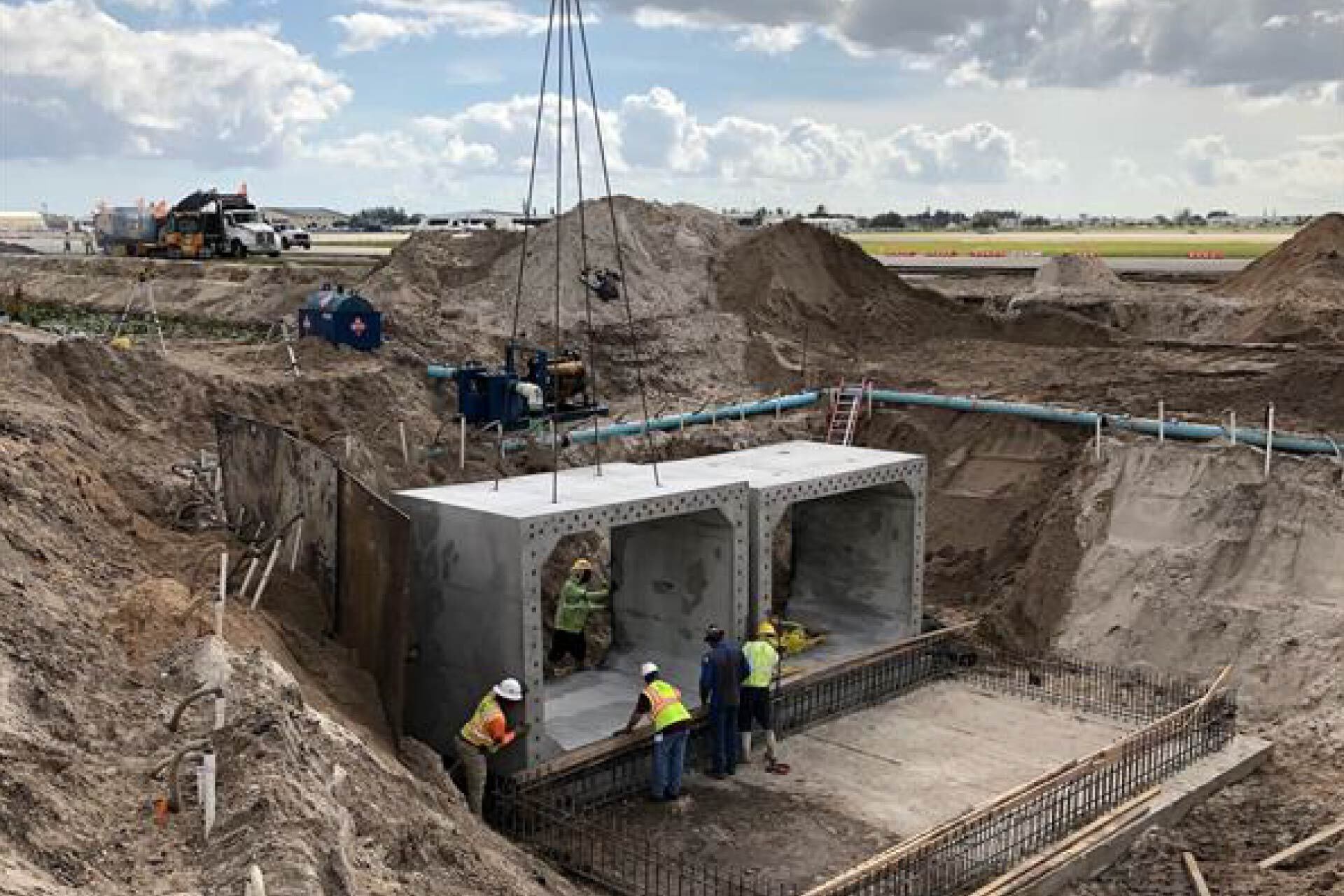
Airports face unique challenges when it comes to building underground structures because the weight and pressure from airplane wheels are much greater than those from regular road vehicles. This means that underground structures at airports need to be much stronger and more carefully designed to avoid problems like subsidence and cracking over time. The right design can also be more cost effective in the long run.
All structures within the safety areas of runways and taxiways need to be designed for the possibility of aircraft wheel loads running over them. Depending on the airport’s level of service and fleet mix, this means aircraft wheel loads anywhere from 9,000 pounds up to 65,000 pounds, where a standard highway HS-20 design loading results in 8,000-pound wheel loads.
Garver uses 3D structural analysis and finite element modeling to design these structures. This modeling helps us choose the most efficient shapes and materials, taking into consideration the types of airplanes that will use the airport and the specific soil conditions at the site. Though the software is common, its use to model aircraft gear loads, groundwater pressure, lateral soil pressure, and fleet mix growth factors is relatively unique in airfield civil projects. This detailed analysis allows us to design structures that not only meet current needs but also forecast future growth, ensuring longevity and cost efficiency.
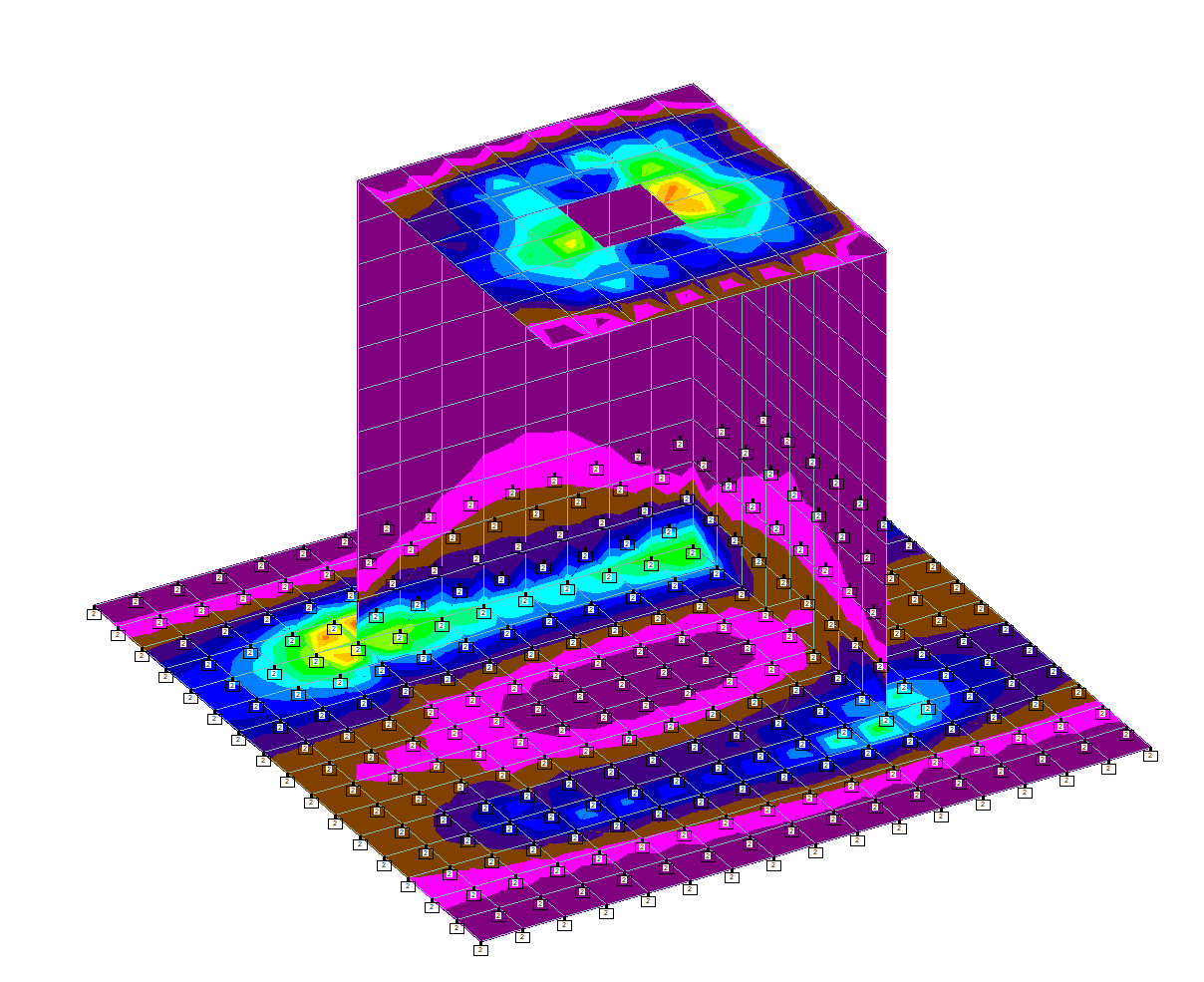
Garver’s approach is particularly beneficial in places like Florida, where large stormwater volume and a high groundwater table call for substantial underground structures and innovative solutions.
Prior to joining Garver, I worked on a project at Palm Beach International Airport where we converted an open channel to an underground box culvert drainage structure to avoid attracting birds and wildlife near the airfield. One underground structure in the project was 30’ x 30’ feet, or essentially the size of a 900-square-foot apartment that connected a double 8-foot by 10-foot box culvert. For the culvert, we used a heavy DOT structure that was off the shelf but still capable of handling aircraft loads, saving costs while ensuring safety and durability.
Sometimes protecting/preserving existing infrastructure is a cost-saving measure. For a project at Birmingham–Shuttlesworth International Airport, I worked with Garver Senior Project Manager Zac Simpson, PE, to tackle the challenge of modifying existing bridge abutment infrastructure that couldn't handle the load of heavier planes. We modeled an 80- by 30-foot concrete slab to distribute the load, which acted almost like a blanket, cushioning the impact on the older infrastructure and saving the client significant costs.
Henderson City - County Airport in Henderson, Kentucky, had flat terrain which presented a different sort of challenge. Due to space constraints, we designed a very shallow box culvert that ran just underneath the taxiway. It had to be thin enough to still fit under the taxiway without necessitating significant regrading of the taxiway. A standard, off-the-shelf precast section would not have worked. By modeling it specifically with a support wall, we managed to fit the structure without altering the taxiway using thin concrete top and bottom slabs in the finite element model, demonstrating the flexibility and precision of our modeling approach.
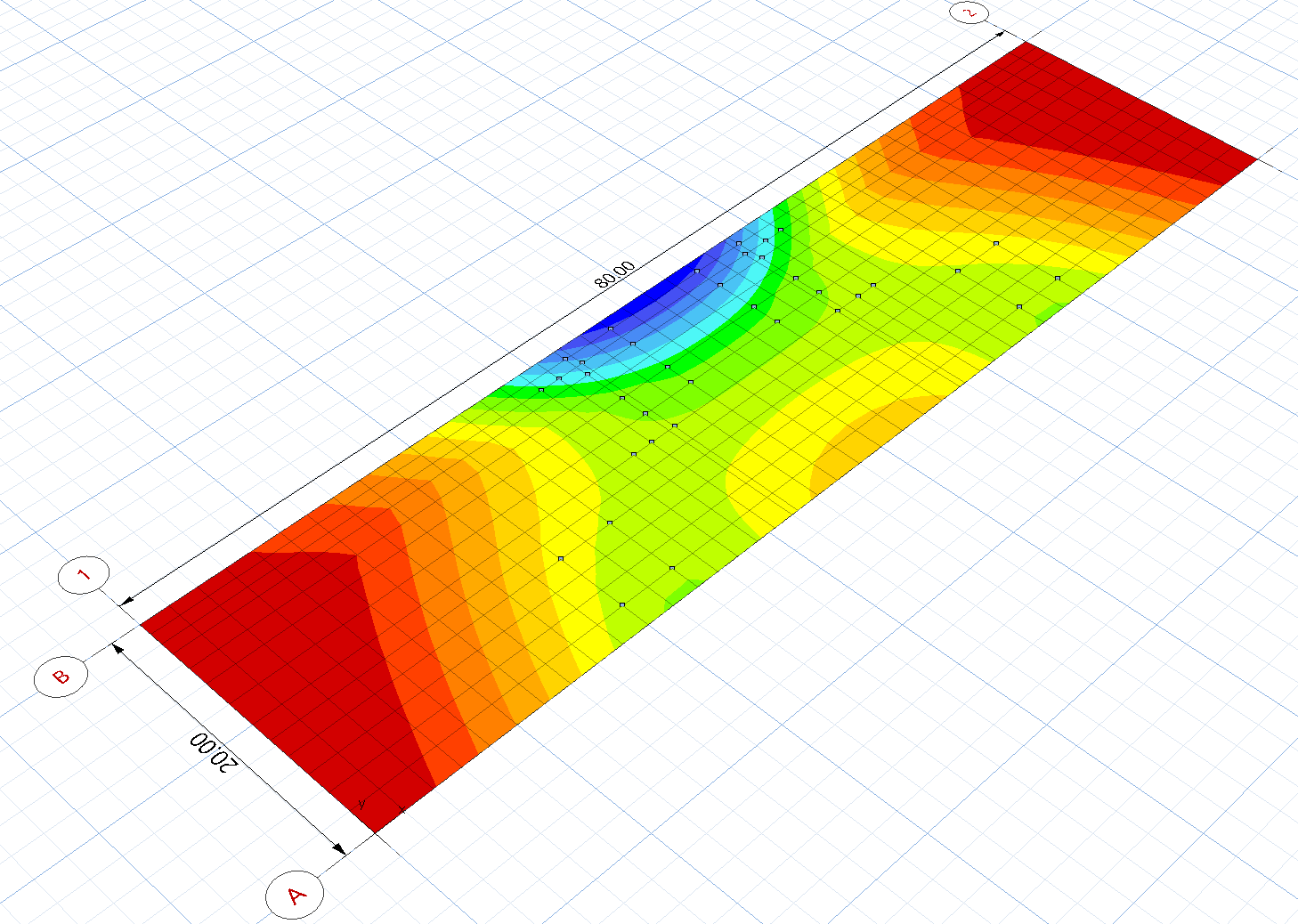
Garver’s innovative approach has become a success story in a niche market. By employing advanced modeling techniques and planning for future growth, we can help airport clients avoid maintenance headaches and serviceability issues for decades after construction.
Share this article